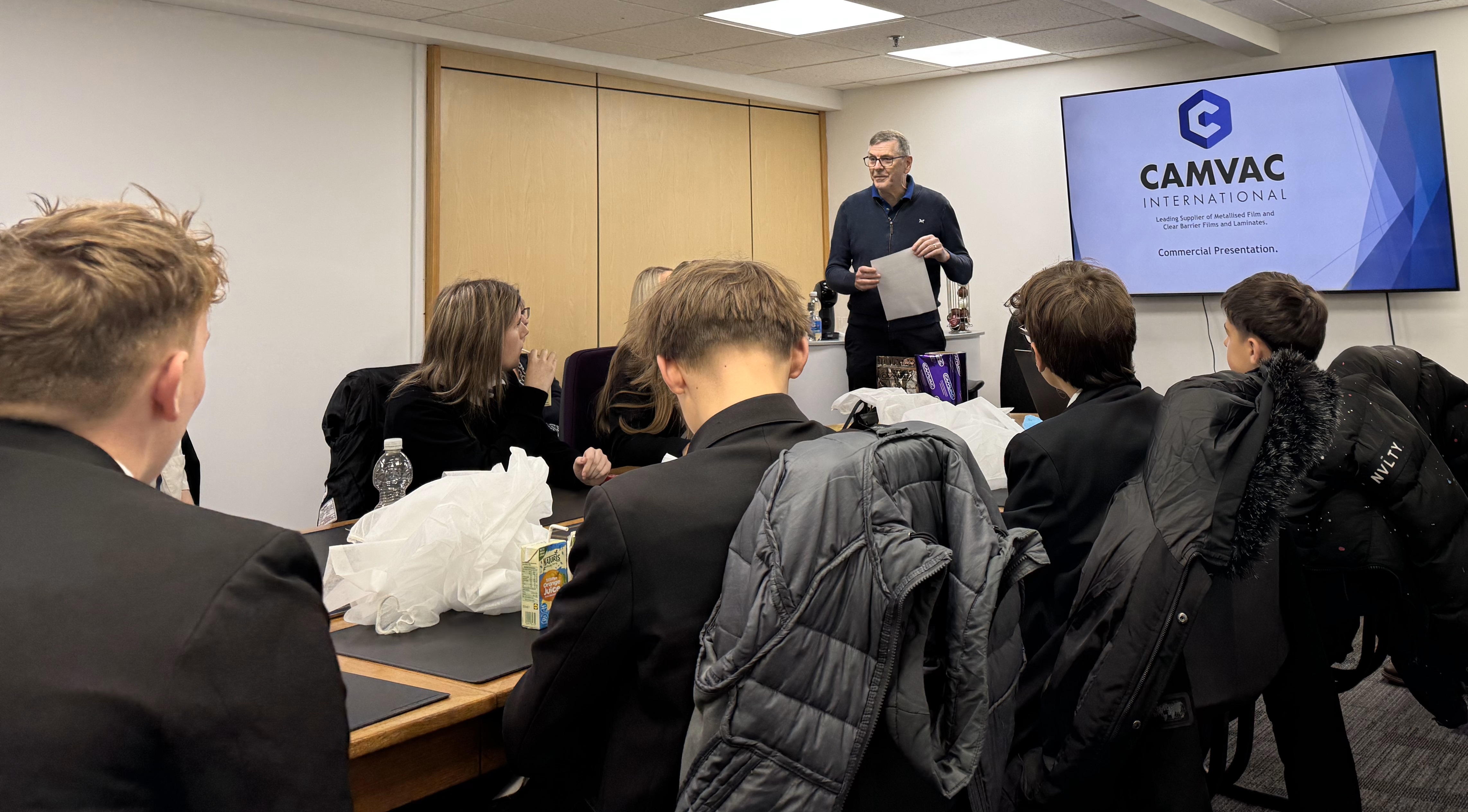
Recently we welcomed pupils from our local Academy for a site visit 📚
CEO Greg conducted a tour of the factory on Brunel Way, this was followed by a presentation from Dan, Dawn & Nicki about their current roles and giving the pupils an insight into potential career paths for the future.
The visit was concluded by our very own Bob Jarman who is in his 50th year at Camvac…Incredible! The perfect example of career progression right there!
Here’s what Bob had to say about ‘Life’ at Camvac 🔽
I did A-levels and 2 years of engineering studies before hearing about the vacancy in the ‘drawing office’ here from my brother (who also did 40 + years)
I was offered the job after a scary interview with the directors(!) and started with Vacuum Research straight from college as a Junior Draughtsman, which meant I was drawing parts of machines for manufacture with a drawing board, pencil and paper! In fact, there were no personal computers and we’d only just got calculators!
I progressed with training and mentoring to become a Design Engineer, part of a team responsible for designing what were then the most advanced metallisers in the world.
I continued to design modifications and improvements for in-house machines and there’s something I’ve designed on most of them still! I even designed one of the slitters we still use.
Part of my role was then in specifying what to buy and evaluating options and then being involved in extending the factory and services to accommodate them.
My next career move was to become Engineering Manager which meant that I then became responsible for maintenance of the plant and machinery with a team of over 20 engineers operating 24/7 at the time.
Managing people was a whole new challenge and required some training and time to settle into the role.
I was still involved in process development, and we were actively licensing some of our technology (Plasma treatment systems ) around the world, mainly Asia and Australia, which kept my interest in design alive.
I was involved in a long-term project to develop our patented IVC process which remains unique in the marketplace, again requiring a lot of engineering design input and working with other engineers to develop control systems etc.
As engineering manager, I enjoyed recruiting and supporting young engineering apprentices, which we have done for over 20 years. Most of these guys have gone on to have successful careers in all fields of engineering, with some still with us.
I’ve always been interested in engineering and science and that’s why I’ve enjoyed most of my time at Camvac – it’s been challenging but rarely dull!
Hopefully some of you may consider a career in engineering – there’s many opportunities out there in all sorts of fields from hands on with spanners and hammers to design and computer programming, so there’s plenty of variety and chances to have a rewarding career.